computer-assisted engineering
What is CAE?
Material mechanics, the calculation of deformation of structures, and fluid dynamics, the calculation of water and air flow, have continued to evolve as computer performance has improved. Engineering simulations that calculate the motion of solids, liquids, and gases are known as computer aided engineering (CAE), and are actively used in the development of plastic products. In the manufacturing of products, molten plastic is poured into molds and formed through various methods, and then cooled and solidified. Since the manufacturing of these molds is time-consuming and costly, it is necessary to use CAE to refine the concept, especially in the early stages of development when various ideas need to be tested.
Example 1, CAE-based food container design
Polypropylene is used in a wide variety of fields, so the simulation targets are wide-ranging. As an example, we show the analysis of deformation when force is applied to a food container. By examining the product's external design, capacity, wall thickness, flange shape, etc., and finding the optimal structure in advance, the number of trial-and-error processes such as mold remaking can be reduced and the development lead time can be shortened.
closet
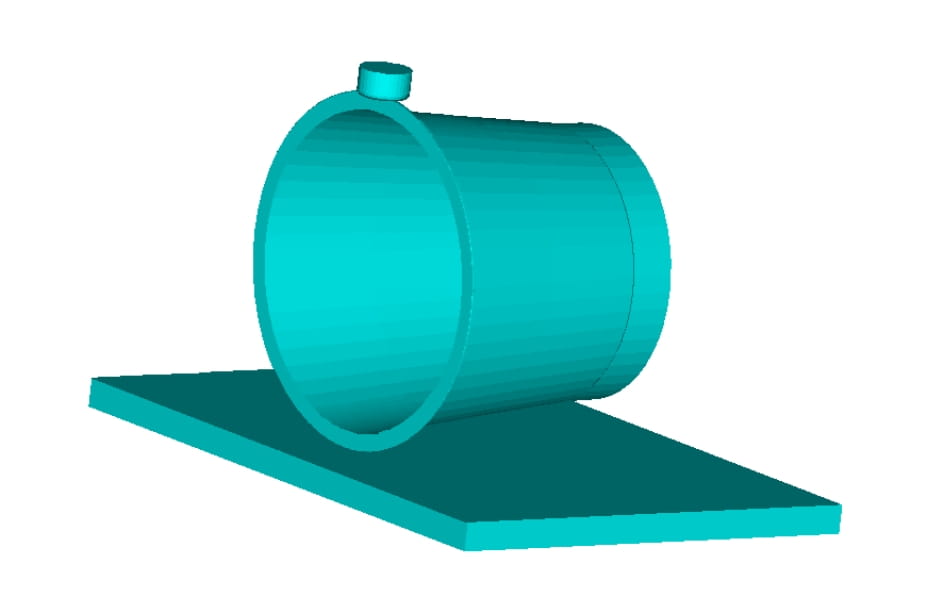
after pushing in
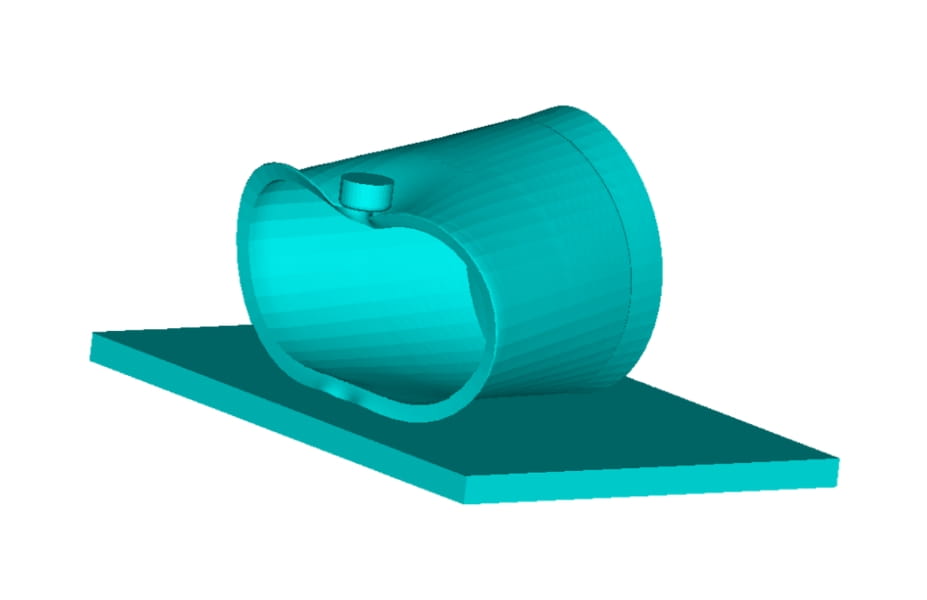
Example 2, Study of a plastic frame that serves as a framework for assembling cooling fans and headlamps in an automobile radiator
Next, we will consider an example of CAE study of a plastic frame that serves as a framework for assembling cooling fans and headlamps in an automobile radiator.
Phase 1 / Optimal product structure to meet rigidity and strength standards
First, we examine the structure to meet product standards for rigidity and strength while keeping the parts within the given design space in the engine compartment.
Distortion in head-on collision with a rigid wall
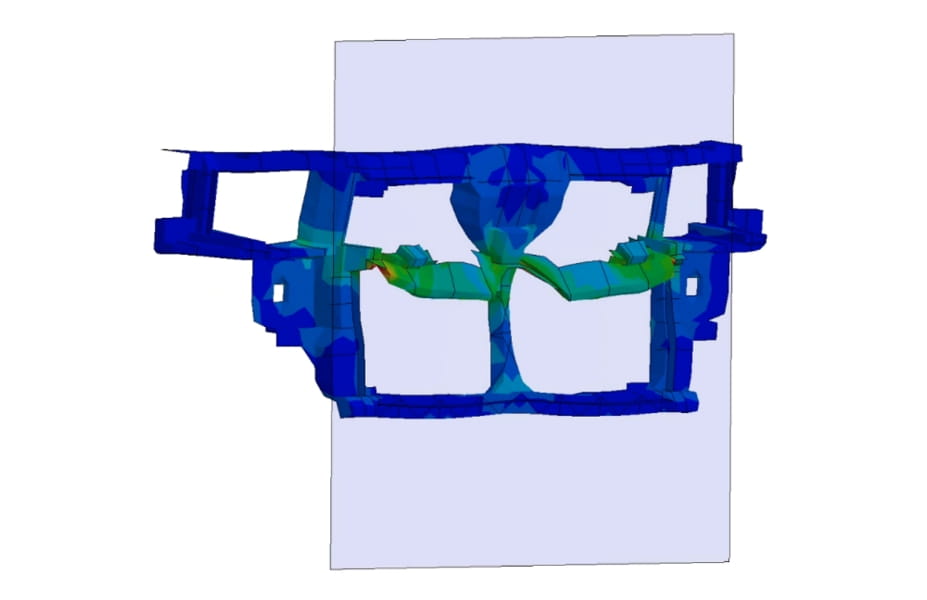
Stress at hood opening and closing

Phase 2 / Study of molding method
Mold design, recommendation of molding machine and molding conditions, proposal of preventive measures against molding defects
After the product structure is determined, cooling tubes and gate layouts are considered and the mold design is finalized. Cooling pipes are designed to cool the product evenly, and gate layouts are designed to suppress short shots and welds. Warpage deformation is also predicted in advance to ensure high quality products. Japan Polypropylene also verifies the accuracy of the analysis to provide highly reliable design support.
Cooling water temperature
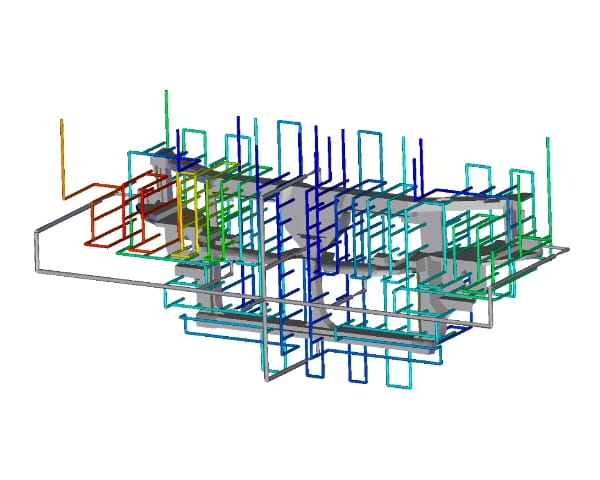
Flow time of molten resin
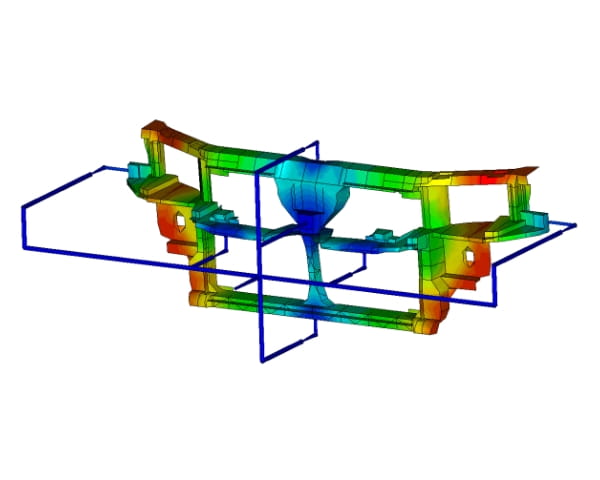
Pressure at completion of filling
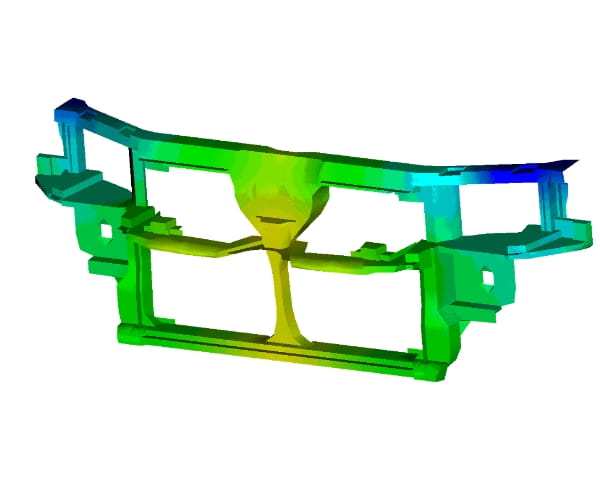
Required clamping force
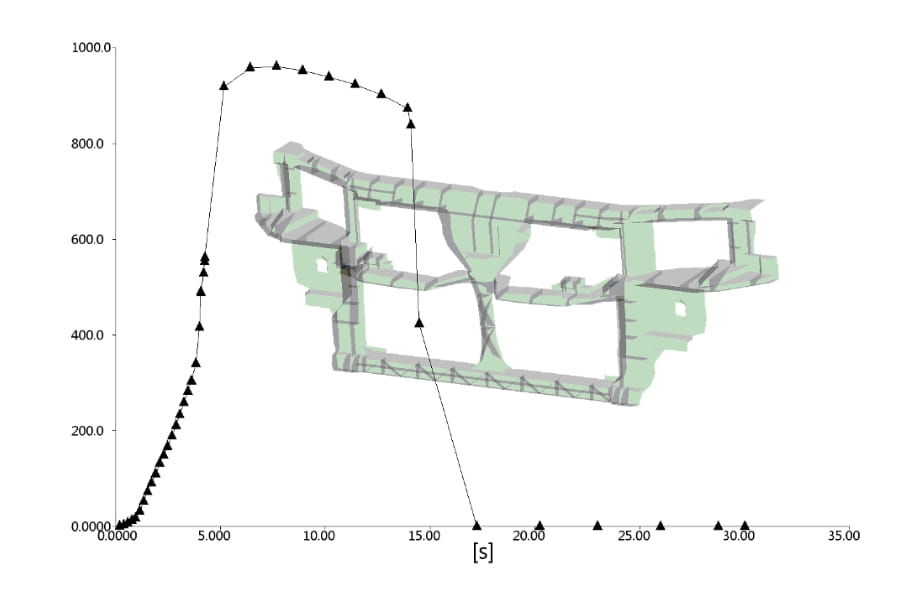
weld
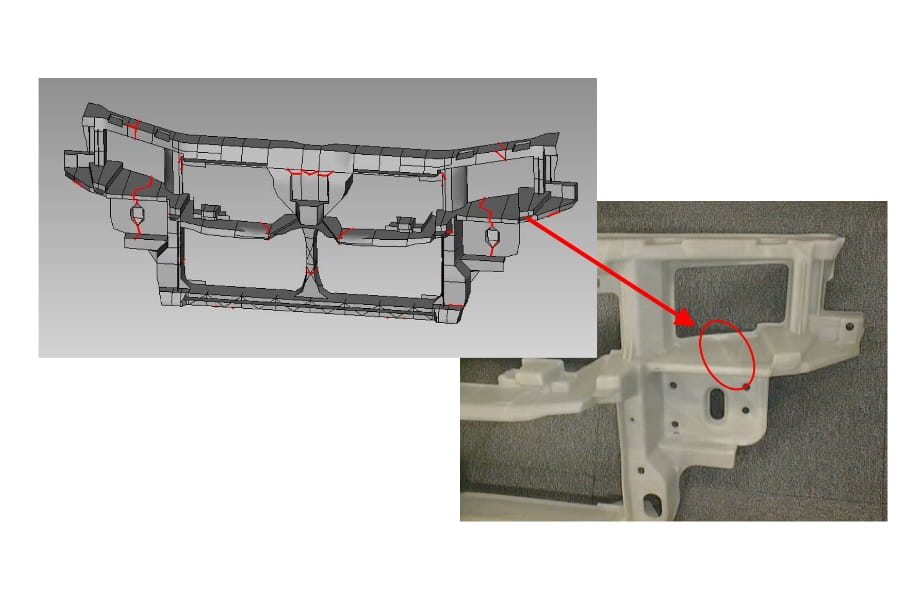
We use CAE to evaluate product structure and productivity to meet rigidity and strength standards, and propose optimal materials through dialogue with our customers.